How to Handle Roadside Inspections: A Trucking Company's Guide
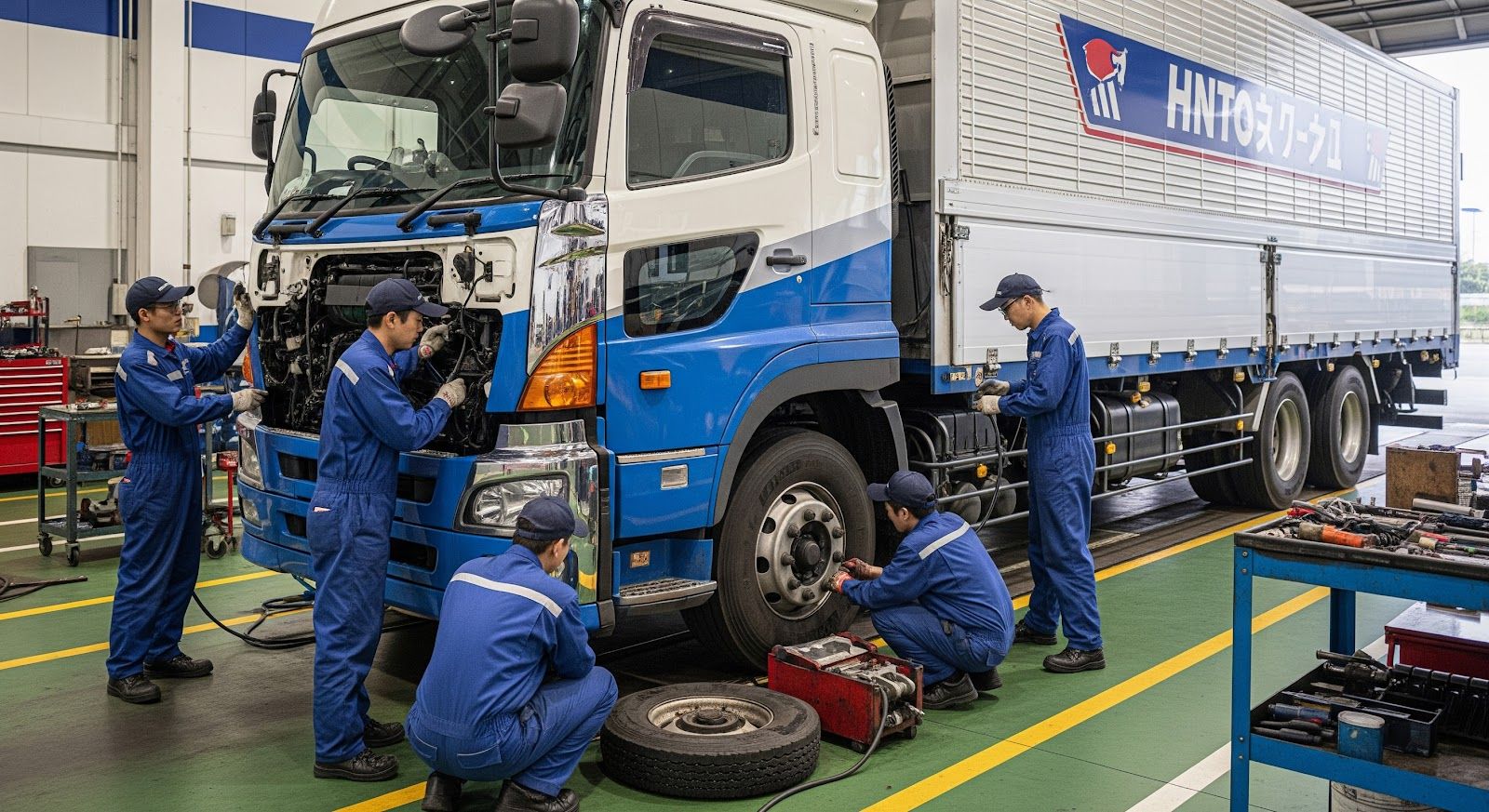
Roadside inspections are a fundamental part of the trucking industry, designed to enhance the safety and compliance of commercial motor vehicles (CMVs) operating on U.S. roadways. These inspections, carried out by state and federal enforcement officials, help ensure that both vehicles and drivers meet the rigorous safety and regulatory standards established by agencies such as the Federal Motor Carrier Safety Administration (FMCSA) and the Department of Transportation (DOT).
Truck drivers must be prepared for these inspections at any time, as they can occur at weigh stations, random checkpoints, or as part of routine traffic stops. Failing an inspection can result in fines, citations, out-of-service orders, or even a negative impact on a driver's Compliance, Safety, and Accountability (CSA) score. Conversely, maintaining compliance with safety regulations can lead to fewer inspections and a better safety record, which benefits both the driver and the company they work for.
The Role of Inspections in Safety and Compliance
The primary goal of roadside inspections is to promote highway safety by identifying and mitigating risks associated with commercial vehicles. These inspections serve several key purposes:
- Ensuring Vehicle Safety: Inspectors thoroughly examine the truck’s critical components, including brakes, tires, lights, steering systems, and suspension. Any defects or malfunctions in these areas can pose serious risks to the driver and other motorists.
- Verifying Driver Compliance: Inspectors review a driver's credentials, including their commercial driver's license (CDL), medical certification, and hours-of-service (HOS) logs to ensure they are operating within legal limits. Fatigue-related violations, such as exceeding allowable driving hours, can lead to serious consequences.
- Checking Cargo Securement and Hazmat Compliance: Proper cargo loading and securement are essential for maintaining stability and preventing load shifts that could lead to accidents. If a driver is transporting hazardous materials (HAZMAT), inspectors will check for proper labeling, placarding, and adherence to hazardous material regulations.
By enforcing these regulations, roadside inspections help reduce accidents caused by vehicle defects, driver fatigue, or improperly secured cargo. They also reinforce the importance of compliance within the trucking industry, ensuring that companies and drivers alike uphold their responsibilities in maintaining road safety.
How Roadside Inspections Are Conducted
Truck drivers should be aware of the process and expectations during a roadside inspection to ensure smooth and efficient compliance. Inspections can range in intensity, from a basic document review to a full-scale vehicle examination. The process typically follows these steps:
- Selection for Inspection:
- A CMV may be pulled over at a weigh station, designated roadside checkpoint, or during a traffic stop.
- Inspections can be random or based on an officer’s observation of potential issues (e.g., visible defects, improper lane usage, or erratic driving behavior).
- Driver Documentation Review:
- The inspector will ask the driver to present essential documents, including:
- Commercial Driver’s License
- Medical Examiner’s Certificate (if required)
- Vehicle registration and proof of insurance
- Hours-of-service logs (electronic or paper)
- Bill of lading and other transport-related paperwork
- If transporting hazardous materials, additional documentation such as shipping papers, emergency response information, and placarding compliance will be checked.
- The inspector will ask the driver to present essential documents, including:
- Vehicle Inspection:
- Inspectors conduct a systematic check of the vehicle’s major safety components, which may include:
- Brakes
- Tires and Wheels
- Lighting System
- Steering and Suspension
- Fuel and Exhaust System
- Cargo Securement
- Inspectors conduct a systematic check of the vehicle’s major safety components, which may include:
- Violation Assessment and Enforcement Actions:
- If no violations are found, the driver receives a pass and may continue their route.
- If minor violations are discovered, the driver may be issued a citation or warning, with instructions for corrective action.
- If severe safety violations are detected, the vehicle or driver may be placed out of service (OOS) until the issues are resolved.
How Truck Drivers Can Prepare for Inspections
To minimize the risk of violations and ensure a smooth roadside inspection process, truck drivers should adopt a proactive approach to compliance:
- Perform Regular Pre-Trip and Post-Trip Inspections: Conduct thorough vehicle checks before and after each trip, addressing any maintenance concerns promptly.
- Maintain Up-to-Date Documentation: Ensure all required paperwork is current and readily accessible. Electronic logging devices (ELDs) should be functioning properly.
- Follow Hours-of-Service Rules: Avoid exceeding HOS limits and ensure logs accurately reflect duty status.
- Secure Cargo Properly: Double-check that all loads are safely secured and within legal weight limits.
- Stay Professional and Cooperative: A positive and cooperative attitude with inspectors can make the process smoother.
By following these best practices, truck drivers can reduce the likelihood of violations, maintain a clean safety record, and ensure compliance with industry regulations.
Key Components of Roadside Inspections
Roadside inspections cover several critical aspects of CMV safety. Each inspection involves a comprehensive review of multiple elements to determine compliance with regulatory requirements. The main components include:
1. Vehicle Inspection Points
Ensuring that CMVs are mechanically sound is a key part of roadside inspections. Vehicle inspection points include:
- Brake System: Proper brake performance is essential for vehicle safety. Inspectors check for worn-out brake pads, air leaks, and adequate brake response times.
- Tires and Wheels: Inspections assess tread depth, tire pressure, and signs of uneven wear, which may indicate alignment or weight distribution issues.
- Lights and Reflectors: All exterior lights, including headlights, brake lights, and turn signals, must function properly. Reflectors must be intact to ensure visibility.
- Steering and Suspension: A functioning steering system and stable suspension are crucial for safe maneuvering. Inspectors check for loose or broken components.
- Exhaust and Emission Systems: Inspections confirm that the exhaust system meets environmental and noise pollution standards.
- Leaks and Fluid Levels: Fuel, oil, and coolant leaks can create hazardous conditions. Inspectors ensure that these fluids are at appropriate levels and not leaking.
2. Driver Compliance Verification
Inspectors also assess whether drivers are qualified and following regulations by reviewing the following:
- Commercial Driver’s License: Drivers must carry a valid CDL corresponding to the type of vehicle they are operating.
- Medical Certificates: Drivers must possess a valid medical certificate to confirm they meet the physical requirements necessary for operating a CMV.
- Hours of Service Logs: Electronic logging devices or paper logs must be up-to-date to ensure compliance with federal HOS regulations, preventing driver fatigue.
- Alcohol and Drug Testing Compliance: Random drug and alcohol tests may be required, and failure to comply can lead to violations and penalties.
3. Cargo and Safety Requirements
Properly secured cargo is crucial for safe transportation. Inspections focus on:
- Load Securement: Cargo must be properly restrained to prevent shifting or falling during transit. Straps, chains, and tie-downs are inspected for wear or damage.
- Hazardous Materials Compliance: If the vehicle is transporting hazardous materials, inspectors check whether the load is properly labeled, documented, and secured as per federal guidelines.
- Weight Limits: Vehicles must not exceed the gross vehicle weight (GVW) limit to prevent road damage and safety hazards.
Understanding the Different Levels of DOT Roadside Inspections
Inspections are categorized into different levels, each with a distinct focus, ranging from a simple document check to an in-depth review of the vehicle’s mechanical condition.
Level I: North American Standard Inspection
The Level I inspection is the most comprehensive and rigorous roadside inspection. It involves a thorough review of both the driver’s credentials and the vehicle’s mechanical condition. Inspectors will check the following:
- Driver Documentation
- Vehicle Inspection
A vehicle or driver that fails to meet compliance standards during a Level I inspection may be placed out of service until the necessary corrections are made.
Level II: Walk-Around Driver/Vehicle Inspection
The Level II inspection is similar to Level I but does not require the inspector to crawl under the vehicle. Instead, the inspector evaluates components that are visible during a walk-around inspection. The primary focus is on:
- Reviewing driver documentation
- Checking the vehicle’s exterior for mechanical defects
- Inspecting cargo securement and hazardous materials compliance
This type of inspection is slightly less intensive than Level I but still ensures that the vehicle and driver meet safety standards.
Level III: Driver-Only Inspection
A Level III inspection focuses solely on the driver’s compliance with regulations. The inspector will verify:
- CDL validity
- Medical certificates
- Driver logbooks and HOS compliance
- Seat belt usage
- Drug and alcohol records (if applicable)
- Compliance with other driver-related regulations
This type of inspection ensures that drivers are legally qualified to operate their vehicles and are adhering to necessary safety requirements.
Level IV: Special Inspections
Level IV inspections are typically one-time inspections conducted to investigate a specific issue or regulatory concern. These inspections may be used for:
- Investigating trends or suspected violations
- Validating regulatory compliance initiatives
- Conducting research studies
Since Level IV inspections are targeted, they may focus on a specific aspect of vehicle or driver compliance rather than a general inspection.
Level V: Vehicle-Only Inspection
A Level V inspection involves a complete check of a vehicle’s mechanical fitness without the driver being present. This type of inspection is commonly conducted at a carrier’s terminal or maintenance facility. Inspectors will examine:
- Brake system
- Fuel system
- Exhaust system
- Suspension and steering components
- Cargo securement
Level V inspections are often required for compliance reviews or fleet audits.
Level VI: Enhanced NAS Inspection for Radioactive Shipments
Level VI inspections are specialized inspections for vehicles transporting radioactive materials. These inspections involve:
- A thorough review of hazardous materials documentation
- Verification of proper packaging and placarding
- Contamination checks and radiation monitoring
- Compliance with all Level I inspection items
Due to the potential risks associated with transporting radioactive materials, Level VI inspections are highly stringent and must be passed before the shipment is allowed to continue.
Understanding the Consequences of Failing a Roadside Inspection
Preparation for roadside inspections is not merely about meeting legal requirements; it’s about safeguarding the efficiency, safety, and reputation of a carrier’s operations.
The potential impacts of failing a roadside inspection include:
- Service Interruptions – Vehicles with critical violations may receive out-of-service orders, preventing them from continuing their route until all issues are resolved. This can lead to substantial delays, customer dissatisfaction, and lost revenue.
- Fines and Citations – Non-compliance with safety regulations often results in costly fines, which vary depending on the severity and frequency of the violations.
- Increased CSA Scores – Poor inspection results can increase a carrier’s Compliance, Safety, Accountability score, leading to heightened enforcement actions, frequent inspections, and increased insurance costs.
The Importance of Proactive Compliance
Understanding the consequences of a failed roadside inspection underscores the importance of proactive compliance. Carriers and drivers can take several steps to reduce the risk of violations, including:
- Regular vehicle maintenance – Conducting thorough pre-trip and post-trip inspections can help identify and fix mechanical issues before they lead to violations.
- Driver training and compliance – Ensuring drivers are well-versed in regulations, including Hours of Service requirements and proper cargo securement, can prevent common compliance errors.
- Accurate record-keeping – Keeping up-to-date logbooks, vehicle maintenance records, and licensing information can prevent documentation-related citations.
- Using technology for monitoring – Electronic logging devices, GPS tracking, and fleet management software can help carriers maintain compliance and proactively address potential violations.
By staying ahead of compliance requirements, carriers can avoid unnecessary penalties, maintain a strong industry reputation, and ensure smooth business operations.